All of the laboratories are equipped with good quality apparatus, have enough space for conducting experiments and are properly ventilated and illuminated.
Computer Aided Modelling Lab
This laboratory focuses on the modelling of different mechanical components. It is used for designing and visualizing mechanical parts and assemblies. This lab is essential for developing precise and efficient mechanical designs, enhancing student’s proficiency in modern engineering tools.
LIST OF EXPERIMENTS
COURSE OUTCOMES: At the end of the course, the student will be able to:
- Draw complex geometries of machine components in sketcher mode.
- Model a part, surface and assembly using Computer-Aided Design software.
- Create complex engineering assemblies using appropriate assembly constraints.
- Develop different views to understand the difficulties in perspective projection.
- Communicate effectively the geometry and intent of design features.
Computer Aided Analysis Lab
In this the students can be able to analyze different mechanical components of the machinery using ANSYS software. Students can be able to perform the structural, thermal analysis. This laboratory also facilitates the student to do project works.
LIST OF EXPERIMENTS
Kinematics and Dynamics Lab
The Kinematics and Dynamics Laboratory is an essential component of the M.Tech. Engineering Design curriculum. It is dedicated to the experimental study of mechanical systems. It is experimentally discussed about the natural frequency of various mechanical systems, conducting static and dynamic balancing of rotating components and exploring the gyroscopic effects in different mechanical setups.
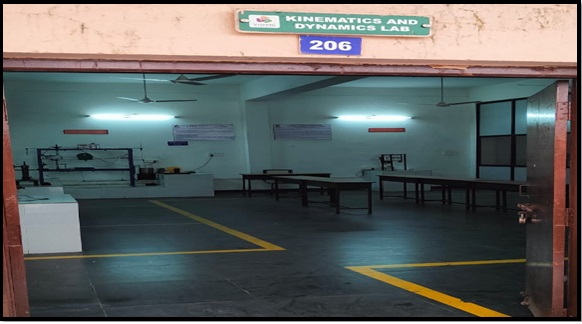
LIST OF EXPERIMENTS
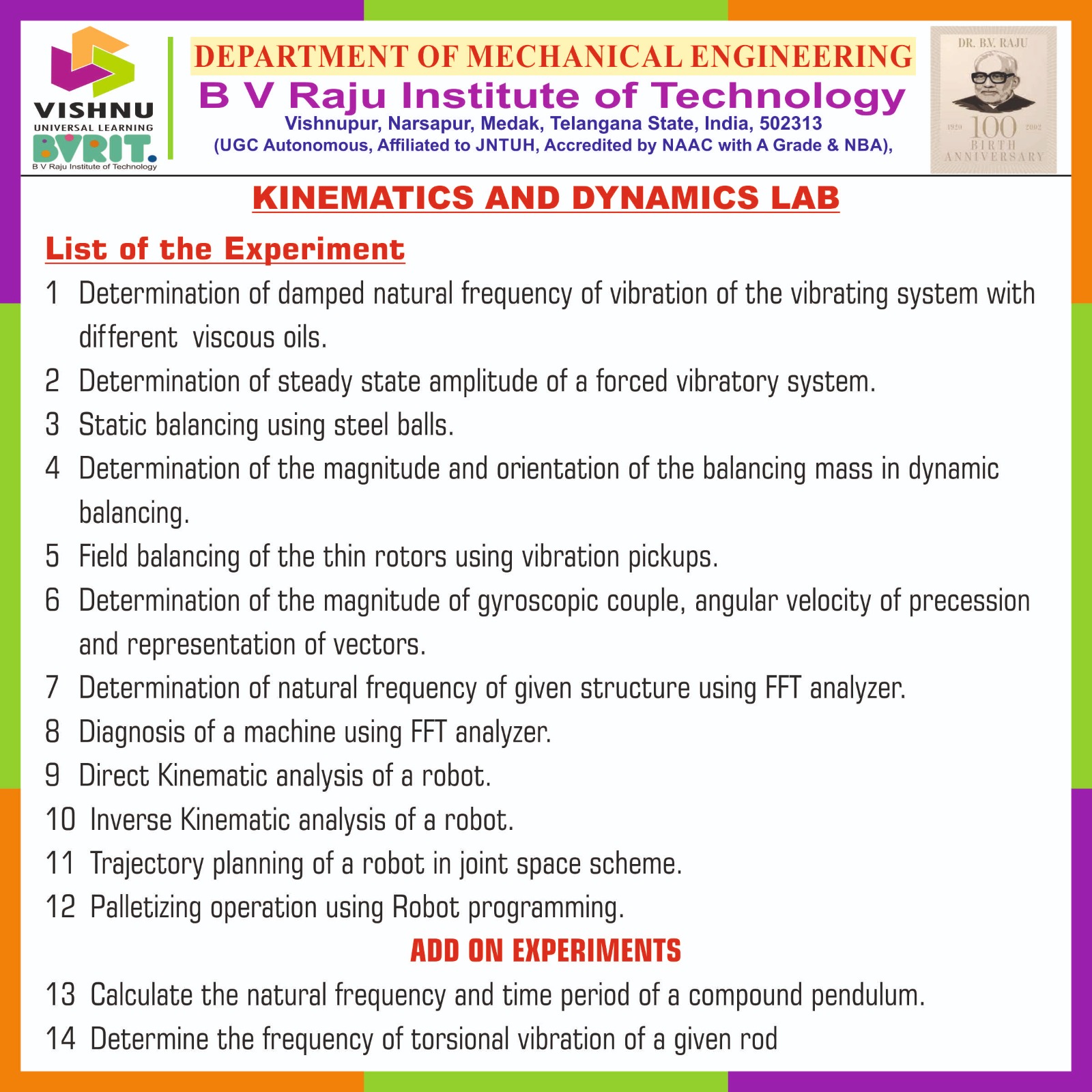
COURSE OUTCOMES: At the end of the course, the student will be able to
- Predict damped natural frequency of vibration of the vibrating system
- Determine the steady state amplitude of a forced vibratory system.
- Identify Static balancing using steel balls.
- Determine the magnitude and orientation of the balancing mass in dynamic balancing.
- Determine the natural frequency of given structure using FFT analyzer.
- Extent the knowledge in various kinematic analysis and summarize the knowledge in robot programming.
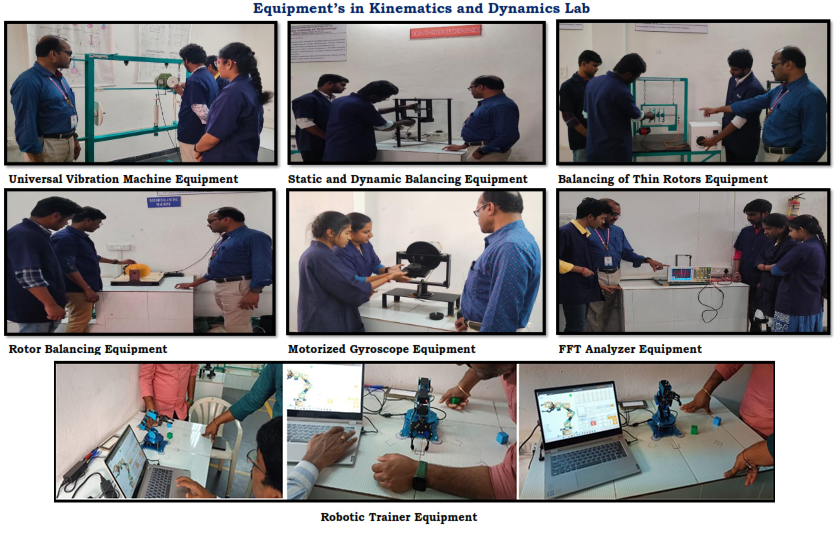
Advanced Technical Skill Lab
To develop the interpersonal skill of the students in various manner. The students have to prepare a working prototype on any idea of their interest related to Mechanical Engineering or (with interdisciplinary approach) during the semester to gain experience and to develop practical approach. The activities under special lab can be undertaken individually or in groups. Students have to submit a report along with a power point presentation, which will be evaluated by a committed constitute by Head of the Department and External Examiner at end of the semester.